Since Rune Skagsoset and the rest of the team started using tablets in their wheel loaders, the raw materials team has been able to positively influence both the fertiliser quality and their own working day. Now, they use a specially adapted dashboard to control the delivery of one million tonnes of raw materials in the right quality to Yara Porsgrunn’s three turnkey fertiliser factories.
Eliminating errors
The statistics clearly show that, within just a few months, incorrect deliveries of raw materials have been eliminated.
“I don't think there have been any incorrect loads or misunderstandings since we implemented the tablet solution in April,” Rune explains. "And when there are no incorrect deliveries, the fertiliser quality improves. Previously, we spent a lot of time finding out why errors occurred. Now, I can quickly spot quality errors, make adjustments and spend less time on troubleshooting. The raw material we use is expensive and is shipped a long way by sea to Herøya, so it also makes good financial sense that we can use the right raw materials in fertiliser production every time."
Rune's Norwegian nickname “kalikjører” (potassium driver) is inspired by the raw material used for fertiliser, which mainly consists of different types of potassium salts.
Digital pilots are the pioneers
Rune and the rest of the raw materials team worked closely with IT and automation collegues at Yara to adapt the information displayed on the dashboard to ensure efficient and error-free transfer of raw materials from ship to turnkey fertiliser factory.
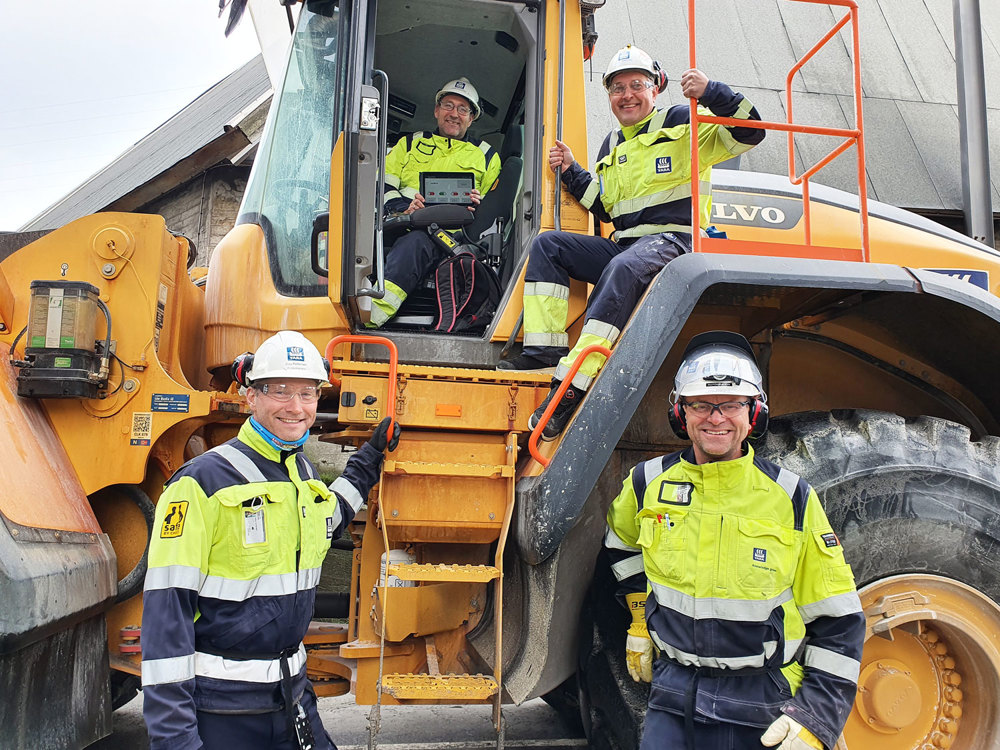
The IT and automation team are the supplier. “When Rune says jump, we jump and execute,” says “IT developer” Dag Pettersen, with a twinkle in his eye. "We use a PIM (Process Information Management) system, but this is the first time we've built up screens via dashboards, so there have been a few small challenges. The screens are now working very well, and it's really easy to add additional functions and change interfaces. The system has buttons, graphs and value displays added as a complete package to the PIM system delivered by Porsgrunn firm Bazefield. "It's really easy to adapt just by pressing buttons and values on the screen," explains Pettersen.
New work routines
Rune Skagsoset also uses his tablet to manage his own working day in the wheel loader.
"It gives me an overview, and I also get real-time information directly from the production system, and can see where and which raw materials I need to load. I can quite simply plan my day better. Also my lunch break," Rune laughs. “Planning and communication are the most important benefits.”
Dependent
“You soon start to depend on the tablet in the wheel loader,” says Rune. "I couldn't imagine going back to how it used to be, that was much too cumbersome. Another benefit with the new system is that if the tablet isn't working, we can log in by mobile phone."
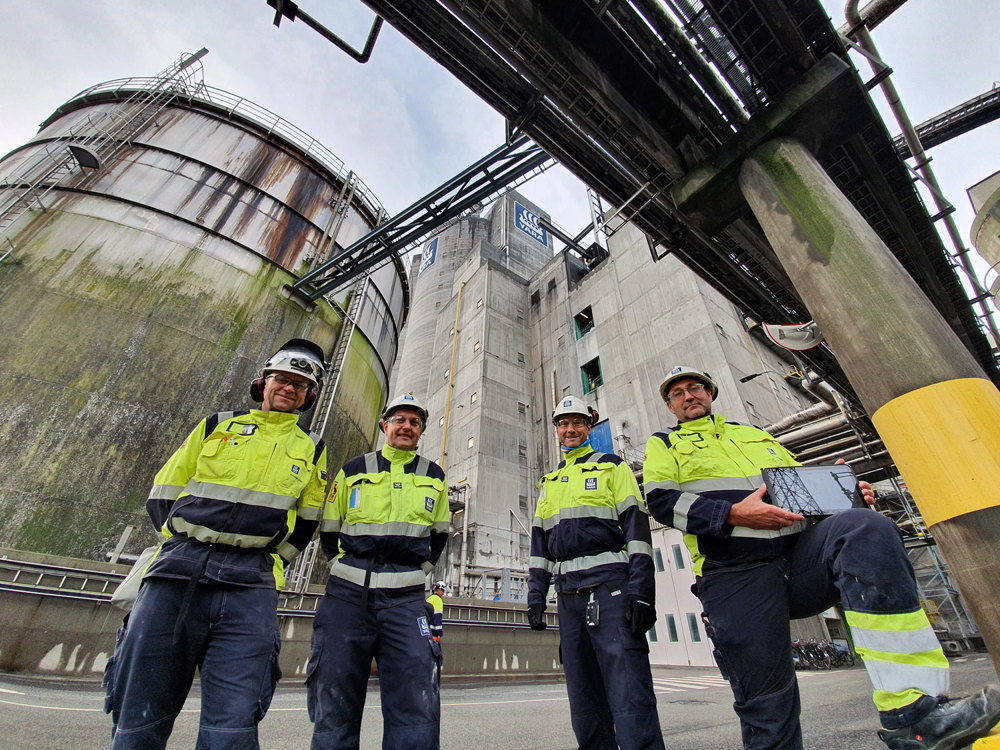
Producing fertiliser is a bit like baking a cake
Rune's job is to supply raw materials to the mineral fertiliser factories.
“Producing fertiliser is a bit like baking a cake,” says Rune. He explains that the main raw material for fertiliser is many different salts, including potassium chloride, potassium sulphate and kieserite, as well as several additives, such as borax, ferrous sulphate, sodium sulphate, MgO and dolomite.
"We source raw materials from mounds delivered in bulk, and dose to ensure sufficient volumes in production. Everything needs to be planned carefully. Sometimes we need to mix several substances together, as the factories have different needs."
Raw material recipes
"The right mix of raw materials is your responsibility?"
"Yes. I get a recipe from the factory stipulating the required volume in tonnes, or the number of buckets. We mix the right raw materials for the right fertiliser quality."
"It’s important to be careful to dose the right type of raw materials when you work for a company that produces the world’s best fertiliser qualities and delivers the widest range of fertiliser qualities from Porsgrunn."
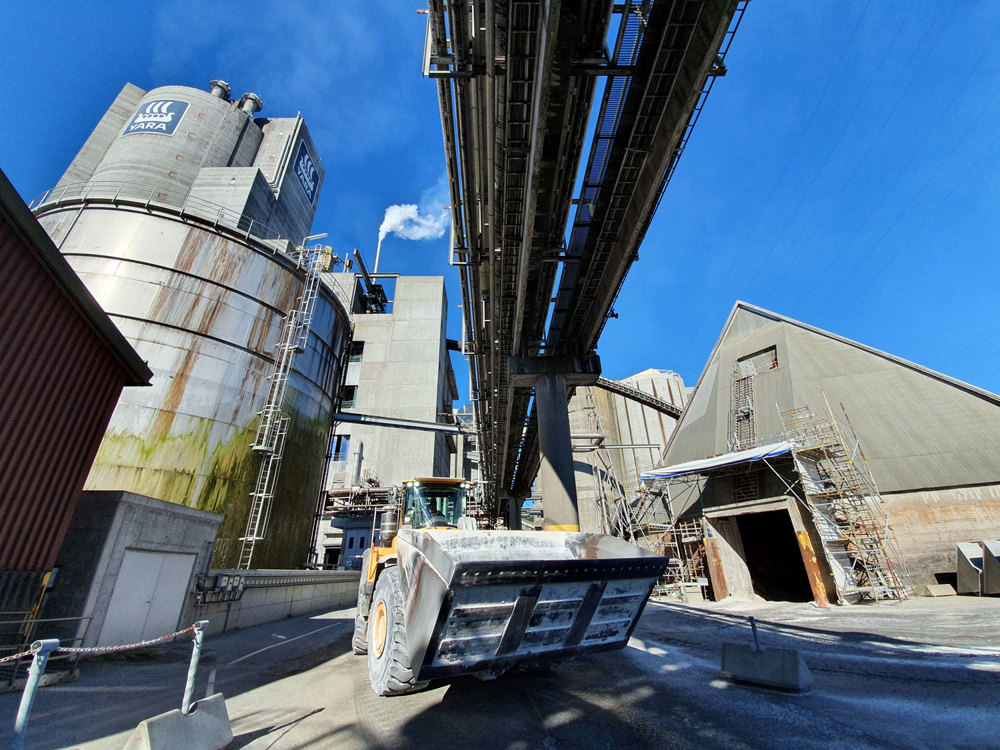
1 million tonnes of salts
“Our consumption is around one million tonnes of salts,” says Rune. "This means quite a few hours, maybe 2,000, spent in the wheel loader in the course of a year."
More tablets
The plan is for more teams to use tablets with customised dashboards in the fertiliser production at Yara Porsgrunn.
“This solution is good for users who handle large volumes,” says Håkon Wærstad, technical manager. He explains that they are planning equivalent systems in two loaders.
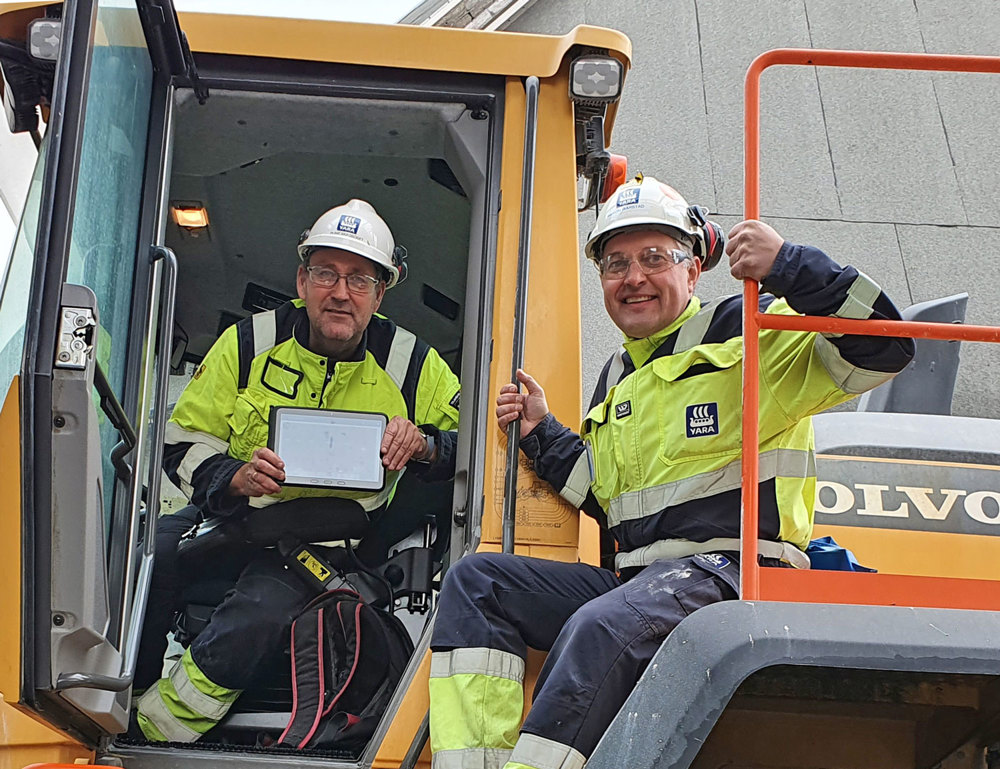
Investment savings
"What is the cost benefit of implementing dashboard systems?"
“We haven't calculated this in fine detail, but I'm confident that eliminating delivery errors, and enabling Rune and his colleagues to have a better working day that they can plan themselves, will cover the investment,” says Wærstad.
"The initial investment was around half a million kroner," he says.
Enabling more, and affordable solutions
At the outset, Wærstad and the IT team at Yara first considered using WiFi, and then 5G, but the solution now used is 4G.
"4G opens up more solutions. And doesn't cost half a million. There is also the cost of a tablet, approx. NOK 6-7,000, and configuration and equipment for installation in a vehicle or loader. I think NOK 50,000 would cover this," says Wærstad.
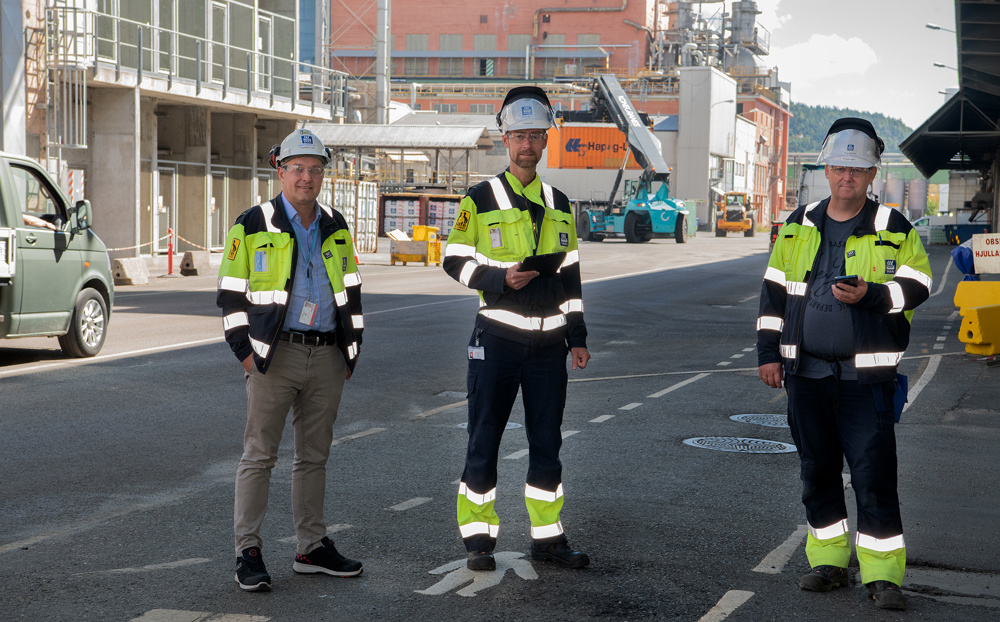
Wærstad and the IT team at Porsgrunn are also involved in the EU’s “5G Solutions” flagship project, in which Yara will use Telenor’s 5G network to undertake a number of tests of equipment in logistics operations at Herøya.
Spin-off
"This project is not part of the EU project, but a spin-off from this strategy. It’s obvious that when we get 5G, the speed will be completely different. Then we can run video if we want to, and have cameras integrated into the system."
“Which is good!” says Rune enthusiastically. "There are some cameras that we would like to have up over time.
21. October 2021