The production of rare earths at Herøya is completely unique and the only one in Europe.
"It is a big milestone for us and for the EU project SecREEts we are part of," say proud pilot partners. "We borrow production streams from Yara and send streams of rare earths back to the value chain." This is a circular industry in practice and is well placed in the environmental accounts, the parties believe.
Establish value chain
SecREEts (EU Grant agreement ID: 776559) wants to establish a competitive and environmentally friendly European value chain based on the phosphate-containing stone Yara uses in its fertilizer production.
"Mining raw materials is an essential part of the cost picture, so here we see a potentially cost-effective value chain by making better use of the raw material," the project parties believe.
Only one in Europa
Today there is no European production of rare earths. The two Norwegian companies Yara and REEtec will thus be the only European producers of these in-demand soils in the green shift.
REEtec, Yara, Sintef and two other European partners received NOK 125 million in EU support to "dig out" and refine the 15 rare earths from Yara's production flows. Two European manufacturers will further process this into products, including super magnets for use in wind turbines and electric cars.
First delivery
"The first container with concentrate of rare earths was delivered this week," says Vibeke Rasmussen from Yara Technology Center proudly. The concentrate is extracted in the production process from the complete fertilizer factory in full operation.
"We have scaled up a plant, from lab, that can handle larger volumes," says Mohan Menon, in Yara Technology. "We go in and "borrow" a small part of the production flow and extract approx. one cubic meter concentrate of rare earths per day."
"Nobody has done this before, so here we learn about technical and financial challenges that can be taken further in a possible full-scale facility," says the project team from Yara.
Why is Yara involved in this?
"It makes sence that we can utilize the raw material better," says Vibeke Rasmussen. "We do not have all the answers now to how we will make use of this, but we will study the pilot phase to find out more about the possibilities. The process does not affect the fertiliser product, so if we can extract this value that others can utilize, it is positive.
Completely unique
It is the start of the process that is unique in the SecREEts project, the project parties say.
"It's what we do here at Herøya that is completely unique in the project. The other two parties in the value chain can use raw materials from several sources," explains Sigve Sporstøl, general manager of REEtec.
"The process plant has been developed in Norway and built over a long period of time here at Herøya. We have operated the demo plant since 2019, and learned the process based on other raw materials. We are now ready with a tailor-made front end in the plant that can process raw materials from Yara. We will spend the next six months fine-tuning the process with raw materials from Yara, and producing materials that will continue in the value chain and become magnets. That will be in 2021," says Sporstøl.
In the long term, REEtec wants to develop the plant to extract raw materials from several sources.
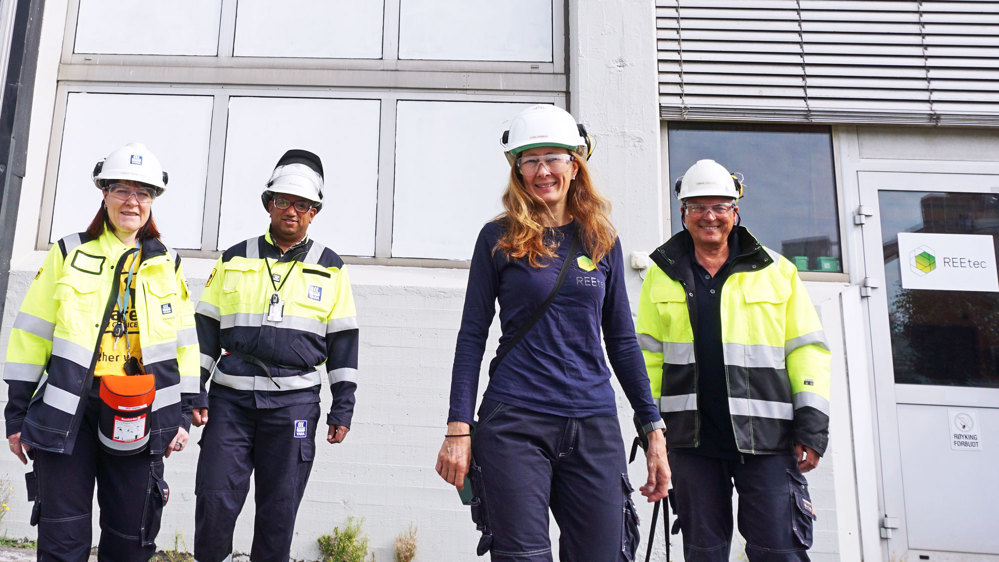
Profitabel business
"The technology we have developed is environmentally friendly and cost-effective compared to other players, therefore everything should be in place to build a profitable business," says the REEtec team, working in parallel to see how an industrial plant could be built.
"Finishing a construction drawing on how to build a full-scale factory, is part of the project," says Sporstøl. "The market is growing strongly, largely due to the demands for magnets used in motors on electric cars," he says.
"The current total market is about 200,000 tonnes. In 2030 the marked will probably be around 300,000 tonnes, or significantly more," Sporstøl believes. "China will hardly be able to produce enough, and there will be a need for new capacity. The size of a plant we operate here is a couple of thousand tons and more. The technology is module-based, and to a certain extent it can be expanded if we need to," he says.
Author/photo: Siri Krohn-Fagervoll
20. August 2020